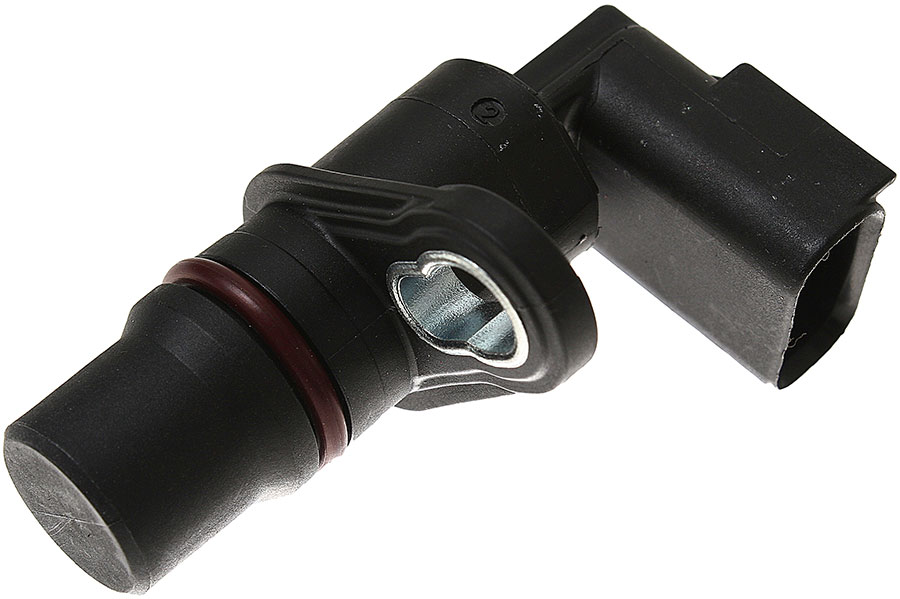
Dans toute unité de puissance moderne, il existe toujours un capteur de position du vilebrequin, sur la base duquel les systèmes d'allumage et d'injection de carburant sont construits.Découvrez tout sur les capteurs de position de vilebrequin, leurs types, leur conception et leur fonctionnement, ainsi que sur le choix et le remplacement corrects de ces dispositifs dans l'article.
Objectif et place du capteur de position du vilebrequin dans le moteur
Capteur de position du vilebrequin (DPKV, capteur de synchronisation, capteur de démarrage de référence) - un composant du système de commande électronique du moteur à combustion interne ;Un capteur qui surveille les caractéristiques de performance du vilebrequin (position, vitesse), et assure le fonctionnement des principaux systèmes du groupe motopropulseur (allumage, puissance, distribution de gaz, etc.).
Les moteurs à combustion interne modernes de tous types sont pour la plupart équipés de systèmes de commande électroniques, qui prennent entièrement en charge le fonctionnement de l'unité dans tous les modes.La place la plus importante dans de tels systèmes est occupée par les capteurs - des dispositifs spéciaux qui suivent certaines caractéristiques du moteur et transmettent des données à l'unité de commande électronique (ECU).Certains capteurs sont essentiels au fonctionnement du groupe motopropulseur, notamment le capteur de position du vilebrequin.
DPKV mesure un paramètre : la position du vilebrequin à chaque instant.Sur la base des données obtenues, la vitesse de l'arbre et sa vitesse angulaire sont déterminées.En recevant ces informations, l'ECU résout un large éventail de tâches :
● Détermination du moment PMH (ou PMH) des pistons du premier et/ou quatrième cylindres ;
● Contrôle du système d'injection de carburant - détermination du moment d'injection et de la durée des injecteurs ;
● Contrôle du système d'allumage - détermination du moment d'allumage dans chaque cylindre ;
● Contrôle du système de calage variable des soupapes ;
● Contrôle du fonctionnement des composants du système de récupération des vapeurs de carburant ;
● Contrôle et correction du fonctionnement d'autres systèmes liés au moteur.
Ainsi, DPKV assure le fonctionnement normal du groupe motopropulseur, déterminant pleinement le fonctionnement de ses deux systèmes principaux - l'allumage (uniquement dans les moteurs à essence) et l'injection de carburant (dans les injecteurs et les moteurs diesel).En outre, le capteur s'est avéré pratique pour contrôler d'autres systèmes moteurs dont le fonctionnement est directement ou indirectement synchronisé avec la position et la vitesse de l'arbre.Un capteur défectueux peut perturber complètement le fonctionnement du moteur, il faut donc le remplacer.Mais avant d'acheter un nouveau DPKV, vous devez comprendre les types de ces appareils, leur conception et leur fonctionnement.
Types, conception et principe de fonctionnement du DPKV
Quels que soient le type et la conception, les capteurs de position du vilebrequin se composent de deux parties :
● Capteur de position ;
● Le disque maître (disque de synchronisation, disque de synchronisation).
DPKV est placé dans un boîtier en plastique ou en aluminium, qui est monté au moyen d'un support à côté du disque maître.Le capteur dispose d'un connecteur électrique standard pour la connexion au système électrique du véhicule, le connecteur peut être situé à la fois sur le corps du capteur et sur son propre câble de courte longueur.Le capteur est fixé sur le bloc moteur ou sur un support spécial, il est situé en face du disque maître et en cours de fonctionnement compte ses dents.
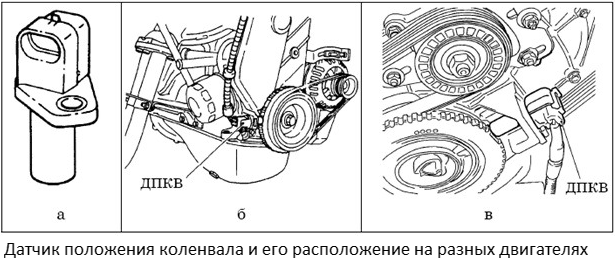
Capteur de position de vilebrequin sur différents moteurs
Le disque maître est une poulie ou une roue, le long de la périphérie de laquelle se trouvent des dents de profil carré.Le disque est fixé rigidement sur la poulie de vilebrequin ou directement sur sa pointe, ce qui assure la rotation des deux pièces avec la même fréquence.
Le fonctionnement du capteur peut être basé sur divers phénomènes et effets physiques, les plus répandus sont des dispositifs de trois types :
● Inductif (ou magnétique) ;
● Basé sur l'effet Hall ;
● Optique (lumière).
Chacun des types de capteurs a ses propres caractéristiques de conception et son principe de fonctionnement.
DPKV inductif (magnétique).Au cœur de l'appareil se trouve un noyau magnétique placé dans un enroulement (bobine).Le fonctionnement du capteur est basé sur l’effet de l’induction électromagnétique.Au repos, le champ magnétique dans le capteur est constant et il n'y a pas de courant dans son enroulement.Lorsque la dent métallique du disque maître passe à proximité du noyau magnétique, le champ magnétique autour du noyau change brusquement, ce qui entraîne l'induction de courant dans le bobinage.Lorsque le disque tourne, un courant alternatif d'une fréquence particulière se produit à la sortie du capteur, qui est utilisé par l'ECU pour déterminer la vitesse du vilebrequin et sa position.
Il s'agit de la conception de capteur la plus simple, elle est largement utilisée sur tous les types de moteurs.L'avantage des appareils de ce type est leur fonctionnement sans alimentation électrique - cela permet de les connecter avec une seule paire de fils directement à l'unité de commande.
Capteur à effet Hall.Le capteur est basé sur un effet découvert par le physicien américain Edwin Hall il y a près d'un siècle et demi : lorsqu'un courant traverse deux côtés opposés d'une fine plaque métallique placée dans un champ magnétique constant, une tension apparaît sur ses deux autres côtés.Les capteurs modernes de ce type sont construits sur des puces Hall spécialisées placées dans un boîtier avec des noyaux magnétiques, et leurs disques maîtres ont des dents magnétisées.Le capteur fonctionne simplement : au repos, il y a une tension nulle en sortie du capteur, au passage de la dent aimantée, une tension apparaît en sortie.Comme dans le cas précédent, lorsque le disque maître tourne, un courant alternatif apparaît à la sortie du DPKV, qui est fourni au calculateur.
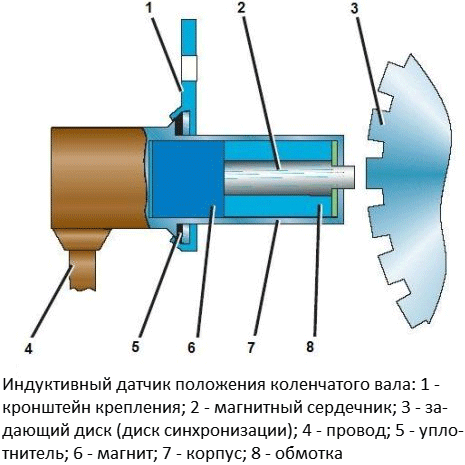
Capteur de position inductif de vilebrequin
Il s'agit d'un capteur plus complexe, qui offre cependant une précision de mesure élevée sur toute la plage de vitesse du vilebrequin.De plus, le capteur Hall nécessite une alimentation séparée pour fonctionner, il est donc connecté avec trois ou quatre fils.
Capteurs optiques.La base du capteur est une paire de source lumineuse et de récepteur (LED et photodiode), dans l'espace entre lesquels se trouvent des dents ou des trous du disque maître.Le capteur fonctionne simplement : le disque, lorsqu'il tourne à des intervalles variables, éclipse la LED, ce qui entraîne la formation d'un courant pulsé à la sortie de la photodiode - il est utilisé par l'unité électronique pour la mesure.
Actuellement, les capteurs optiques sont d'une utilité limitée, en raison des conditions difficiles de leur fonctionnement dans le moteur - forte poussière, possibilité de fumée, contamination par des liquides, saleté de la route, etc.
Des disques maîtres standardisés sont utilisés pour travailler avec des capteurs.Un tel disque est divisé en 60 dents situées tous les 6 degrés, alors qu'à un endroit du disque il n'y a pas deux dents (disque de synchronisation type 60-2) - ce passage est le début de la rotation du vilebrequin et assure la synchronisation du capteur, Calculateur et systèmes associés.Habituellement, la première dent après le saut coïncide avec la position du piston du premier ou du dernier cylindre au PMH ou PMH.Il existe également des disques avec deux sauts de dents situés à un angle de 180 degrés l'un par rapport à l'autre (disque de synchronisation de type 60-2-2), ces disques sont utilisés sur certains types de groupes motopropulseurs diesel.
Les disques maîtres des capteurs inductifs sont en acier, parfois en même temps que la poulie de vilebrequin.Les disques des capteurs Hall sont souvent en plastique et des aimants permanents sont situés dans leurs dents.
En conclusion, on note que le DPKV est souvent utilisé aussi bien sur le vilebrequin que sur l'arbre à cames, dans ce dernier cas, il est utilisé pour surveiller la position et la vitesse de l'arbre à cames et ajuster le fonctionnement du mécanisme de distribution de gaz.
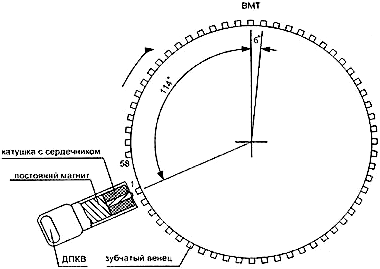
Installation de type DPKV inductif et disque maître
Comment choisir et remplacer correctement le capteur de vilebrequin
Le DPKV joue un rôle clé dans le moteur, les dysfonctionnements des capteurs entraînent une forte dégradation du fonctionnement du moteur (démarrage difficile, fonctionnement instable, diminution des caractéristiques de puissance, détonation, etc.).Et dans certains cas, si le DPKV tombe en panne, le moteur devient complètement inutilisable (comme l'indique le signal Check Engine).Si des problèmes sont décrits avec le fonctionnement du moteur, vous devez alors vérifier le capteur de vilebrequin et, en cas de dysfonctionnement, effectuer un remplacement.
Tout d'abord, vous devez inspecter le capteur, vérifier l'intégrité de son corps, de son connecteur et de ses fils.Le capteur inductif peut être vérifié avec un testeur - il suffit de mesurer la résistance de l'enroulement que le capteur de travail a dans la plage de 0,6 à 1,0 kOhm.Le capteur Hall ne peut pas être vérifié de cette manière, son diagnostic ne peut être effectué que sur un équipement spécial.Mais le moyen le plus simple est d'installer un nouveau capteur, et si le moteur démarre, le problème résidait précisément dans le dysfonctionnement de l'ancien DPKV.
Pour le remplacer, vous devez choisir uniquement un capteur du type installé sur la voiture et recommandé par le constructeur automobile.Les capteurs d'un autre modèle peuvent ne pas se mettre en place ou commettre des erreurs de mesure importantes et, par conséquent, perturber le fonctionnement du moteur.Le DPKV doit être remplacé conformément aux instructions de réparation du véhicule.Habituellement, il suffit de débrancher le connecteur électrique, de dévisser une ou deux vis/boulons, de retirer le capteur et d'en installer un nouveau.Le nouveau capteur doit être situé à une distance de 0,5 à 1,5 mm de l'extrémité du disque maître (la distance exacte est indiquée dans les instructions), cette distance peut être ajustée avec des rondelles ou d'une autre manière.Avec le bon choix du DPKV et son remplacement, le moteur commencera immédiatement à fonctionner, seulement dans certains cas, il sera nécessaire de calibrer le capteur et de réinitialiser les codes d'erreur.
Heure de publication : 13 juillet 2023